To help the customer
The information below will help you to place your order quickly and with high quality.
Certificates
Bureau Veritas certification has certified our factory and production to ISO 9001, ISO 14001 and ISO 45001.
ZINC LAYER THICKNESSES
Zinc layer thickness according to ISO 1461 using the hot-dip galvanizing method:
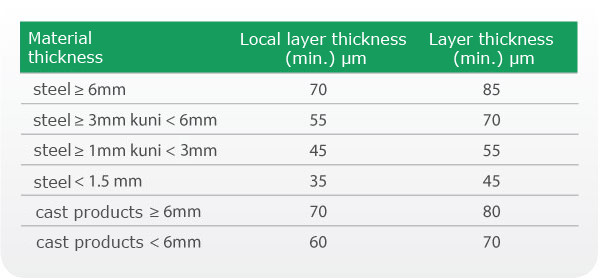
Zinc layer thickness according to ISO 1461 using the centrifugal method:
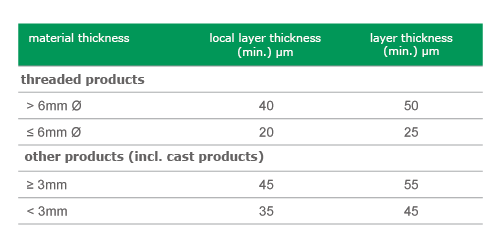
OPENINGS IN THE STRUCTURE
Products must have all the necessary technological openings for zinc plating to allow air to escape and zinc to enter and vice versa.
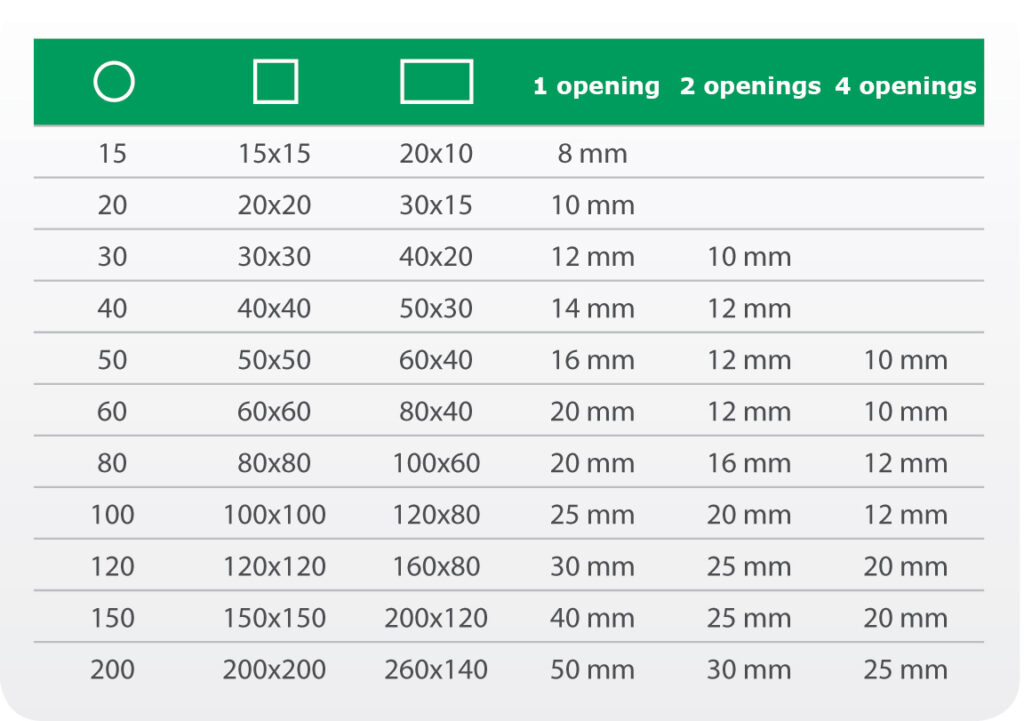
Here you will find solutions for standard structures:
The designer and the manufacturer must ensure that no closed corners are created when adding supports to the structure. The open corner allows the melting agent to reach the entire structure.
Internal supports on such parts must have technological openings at the top and bottom. There must be openings on opposite sides. The containers have the necessary lifting lugs. For larger containers, it is advisable to consult the production manager on the size of the openings and lifting lugs..
Send the following information when placing an order:
- name of the subscriber
- in the case of a first batch, a product drawing with information on the surface area and/or weight of the item.
- Product code of the detail
- quantity of detail
- the type of coating and coating thickness µm required
- desired delivery time
- specific requirements for coating or packaging of the item (if any).
Different variants for the location of technological openings. Make sure that the holes at the other end are on opposite sides.
In the left column, the solutions of the assemblies for which the quality of the hot dip galvanizing is not guaranteed are shown.
Since no molten zinc can get between the parts facing each other, no protective layer is formed and rust will soon start to seep in.
The same condition applies to bolted joints. It is recommended that all bolted joints are made after galvanising to ensure full corrosion protection of the parts.
For such welds, care must be taken to ensure that the technological openings are as close as possible to the welds.
If possible, the ends of the pipes should be left open.
If internal so-called. hidden openings, you must inform the hotline. The size of the concealed holes should be the maximum possible diameter that the pipe will allow.
Care must be taken to avoid closed contours at such junctions. These can be avoided by drilling a hole in the part or by using so-called. step welding
When galvanising such structures, additional supports should be used where possible to ensure that the external appearance is retained after hot-dip galvanising.
The figure shows different solutions for technological openings. Make sure that the openings are on opposite sides of the pipes.
In the case of concealed holes, the diameter of the holes must be the maximum possible diameter.
The figure shows the position of the technological holes in the beam end plates and reinforcing strips.
TERRACE SELECTION
In addition to the corrosion protection provided by zinc coatings, the optical impression of the outer surface of parts – their appearance and structure – is increasingly important. To achieve the desired result, the chemical composition of the steel material used for hot-dip galvanising must meet certain requirements.
If the silicon content is between 0.03…0.12% or above 0.25%,
a particularly violent reaction between iron and zinc and a higher
layer thickness can be expected. The phosphorus content should not exceed 0.020%, as this may
also be followed by a turbulent reaction. It is also worth bearing in mind the interaction between silicon (Si) and phosphorus (P): for cold-rolled material, it should be observed that the contents are Si < 0.03% and Si + 2.5 x P < 0.04% and for hot-rolled material Si < 0.02% and Si + 2.5 x P < 0.09%.
It is the responsibility of the customer to inform the zinc company in writing if there are any discrepancies in the impurity content. Excessive carbon and sulphur content can also lead to a thicker and uneven layer of zinc (scale).
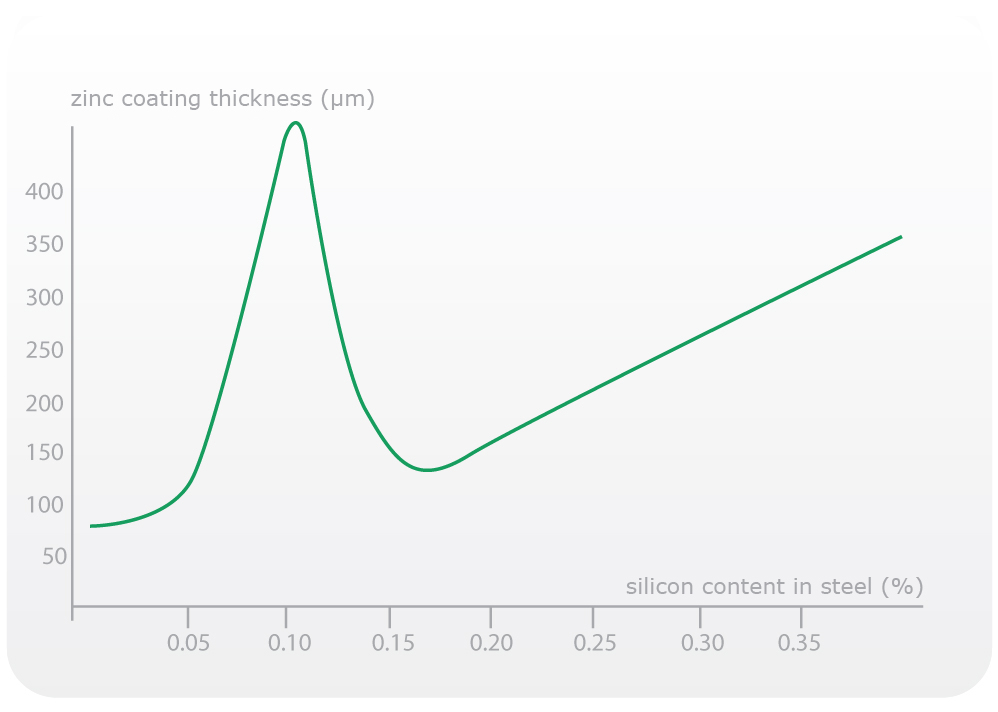
PURITY OF CONSTRUCTION
External surface cleanliness
We do not accept old frames, poles and other old parts for hot dip galvanizing. As this will damage our pre-treatment and also the zinc bath. Products that have been fully or partially painted, varnished, oiled, greased, pre-galvanised, heavily rusted or treated with rust inhibitors must be cleaned before galvanising. It is therefore advisable for the customer to make sure that when purchasing raw materials they are not coated with any of the above mentioned coatings. In order to avoid the formation of defective spots on the zinc coating, the customer must make sure that the outer surface of the steel is free of oil, all types of coatings, tar, grease and various surface protective coatings. The customer must remove any soiled areas of the exterior at his own expense by appropriate treatment of the material and structural parts. Pre-cleaning by the customer of items normally covered with rust is not required. If the items are coated with flammable coatings or contain such residues, the hot dip galvanizing company must be informed in writing before delivery. Painted structures, and in particular old artificial sockets, are particularly at risk of damage, as they very often have non-compliant weld seams and weld cracks and cannot be inspected beforehand. Therefore, possible breakage must be taken into account. If any part of such an object is damaged during the various operations, it will not be compensated. In addition, slight deformation may occur and hot-dip galvanising may also cause warping. We do not accept any claims for restoration, stripping or other work resulting therefrom.
In the case of narrow gaps, joints, etc. between closely spaced flat metal parts, as well as in the case of plastic bundles, poor quality welds (pores, rusty residues) and garden netting, complete paint removal is not possible. It is inevitable that after hot-dip galvanising, corrosive acid and soot residues may come out of the object, which can be identified by reddish-brown streaks. It is therefore advisable to thoroughly clean and cover any damaged areas.
Product labelling
Products must be labelled with a water-soluble dispersion ink. Objects must not be marked with aerosols containing oil paints, grease pastes or silicone, as these must be removed before galvanising, otherwise the areas will remain ungalvanised.
Processing residues
Care must be taken to ensure that only water-soluble emulsions are used when drilling, stamping and pressing galvanised parts. Also, do not use welding consumables containing silicone, as these will partially burn in during welding and will not be removed by the etching acid. Zinc builds up in the unremoved drilling and cutting kerfs and cutting marks during hot-dip galvanising. They are not removed by the hot-dip galvanizing plant. Drilling chips must be completely removed from the inside of the tanks by the customer.
CARE and TREATMENT
To unload goods from trucks, the goods must be placed on bunks or trays so that the forklift’s paws can reach underneath to lift the goods and the maximum package weight could be 2T. We pack the products as we receive them, unless there is a special request. The maximum gauge of the products is 6.80 x 1.30 x 2.50 metres. The maximum weight of a piece is 5.3 tonnes. The pipe or beam can be up to 7m long.
Products that are close to the maximum dimensions please contact us in advance. Please send us a drawing and we will review the hot dip galvanizing possibilities with you.
Products must have any markings removed that are made with paint or marker (including factory markings). Removal of markings, if present, is at extra cost.
At the latest when the products are handed over for processing, the services and specific technical requirements to be provided must be agreed (if possible, a delivery note/letter of transmittal):
- Specific zinc coating thickness (prior consultation recommended)
- Passivation
- Powder coating
- Wounding
- Bundling
- Branding
- Special packaging